Specifying Sustainability in the Construction Industry
Specifying Sustainability in the Construction Industry
Marshall Tufflex have reduced their Scope 3 emissions by focussing on renewables materials for their products without compromising on quality and design. They now call on industry to prioritise more environmentally friendly products during specification.
Sustainable specification is not a new concept. Most are familiar with the practice of ensuring that any timber products included in a specification are sustainably sourced, with full traceability back to a managed forest.
Yet, sadly, the same responsibility is rarely applied when it comes to the specification of plastic products. It’s time for architects and specifiers to place more emphasis on the origins of the plastic products in their specification, to help reduce waste and lower the carbon impact of our buildings.
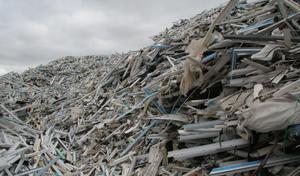
The need for change
More than a third of the UK’s annual waste comes from the construction sector alone, of which 25 million tonnes is disposed at landfill. The UK construction sector is the largest consumer of natural resources, and it is clear that something needs to change. In any strategy that looks to reduce environmental impact, it is vital to consider how construction materials are disposed of and which products are being specified for new builds.
The recycling and reuse of materials has an important role to play in lowering the environmental impact of buildings and achieving a net-zero carbon footprint. Moreover, with the latest law to reduce carbon emission by 78% by 2035 in accordance with the Paris Agreement, it is likely, not long before the construction industry is called on to introduce further measures to reduce its impact.
What are Marshall Tufflex doing?
Marshall Tufflex are constantly looking to improve their own impact within the supply chain. Over 25 years ago, they changed their processes to start using recycled material originating from PVC-U windows in manufacturing their PVC-U products. Since then, they have continued to invest in research and development to refine this process so that they can offer PVC-U products that contain higher amounts of recycled material. In 2020, this figure reached an average of 74% across their range. Not only that, all white Marshall-Tufflex conduit, mini and maxi trunking lengths are currently manufactured using 100% recycled material.
The business uses a compounder machine – a powerful piece of equipment that can process both post-industrial waste (off-cuts from PVC-U window production) and post-consumer waste (from PVC-U windows removed from buildings at the end of their lives). The PVC-U is granulated and processed through the compounder to remove any impurities, resulting in recycled PVC-U material that will be used for new trunking or conduit systems.
What’s more, the use of waste PVC-U windows improves their carbon footprint. Research from the Sustainable Industrial Systems group at the University of Manchester found that a PVC-U window manufactured using recycled content has between 17 and 20 times less embodied carbon than those manufactured from virgin plastic.
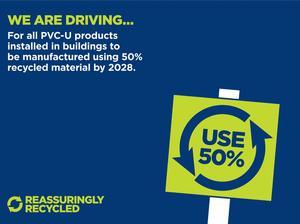
What you can do
It is Marshall Tufflex’s goal that all PVC-U cable management products installed in buildings are manufactured using recycled material by 2028. But this requires support from not only manufacturers and contractors but specifiers as well. Architects and specifiers have a significant influence to drive demand and if PVC-U trunking solutions that are made with a minimum of 50% recycled plastic are more commonly specified, then the hope is that other manufacturers, and indeed, the industry, will follow.
Green does not mean grey
Unfortunately, materials manufactured from recycled plastics often have a stigma attached and are perhaps perceived as lower quality with concerns around colour consistency. However, this is not the case with all products. To ensure consistent quality across all of their products, Marshall Tufflex takes material samples from the production line every hour to check for consistency in colour and surface finish. Further still, the durability of PVC-U plastic from recycled windows is incredibly strong as it is designed to withstand extreme external weather elements.
It is clear that there are huge benefits to writing tighter specifications for plastic products where possible. While Marshall-Tufflex have started to instigate change in the cable management industry, it is also the job of architects and specifiers to drive for change in all levels of construction by specifying products manufactured using more sustainable materials.
Afterall, if the price point is the same and the quality is better, why wouldn’t you specify products with lower environmental impact?
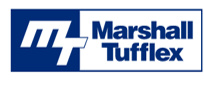
Climate commitment: We have a sustainability team set up internally with a view to looking at issues such as Net Zero by 2050. The team will be reviewing what we need to do to achieve Net Zero and the actions that we need to put in place. Climate Accreditations: ![]() Environment Agency’s Climate Change Levy Scheme (Agreement Identifier: BPF/T00170 v6) Sustainability Statement: For 80 years, we have been pioneering plastic extrusion in the UK and leading the way in areas of product research, development and innovation, especially when it comes to using recycled material. We have been using recycled material in the manufacturing of our products for over 25 years. Drawing on our knowledge and expertise, we continue to innovate and develop new ways to produce superior products that retain their high quality while remaining competitively priced. |
“ It is our goal that all PVC-U cable management products installed in buildings are manufactured using recycled material by 2028. But this requires support from everyone across every level of the electrical industry. Architects and specifiers have a significant influence to drive demand and if PVC-U trunking solutions that are made with a minimum of 50% recycled plastic are more commonly specified, then the hope is that other manufacturers, and indeed, the industry, will follow.”
![]()
Jon Chamberlain